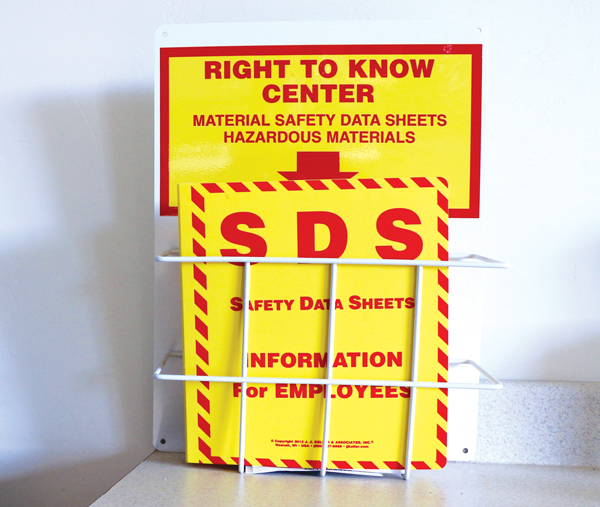
PHOTO: ROAPRODUCTIONS/ISTOCK / GETTY IMAGES PLUS/GETTY IMAGES
The goal of safety data sheets (SDS) is to reduce human and environmental risk by listing potential hazards of daily encountered products, from termiticides to ink. With that goal in mind, today’s SDS providers endeavor to comply with the Globally Harmonized System of Classification and Labeling of Chemicals (GHS), as managed by the United Nations.
SDS provide safety information to any chemical user through compliance with the Occupational Safety and Health Administration’s (OSHA’s) Hazard Communication Program in the U.S., and with the Workplace Hazardous Materials Information System in Canada. Remember, the goal is to protect both the user and the environment. In the pest control industry, we run into some SDS quirks.
INCONSISTENCIES WITH LABELS
One of the most viewed sections of SDS is hazard identification (Section 2), where physical, health and environmental hazards are listed. Arriving at the results is so complicated that most SDS authors use software designed especially for this purpose, where physical and chemical properties are entered, and the hazards are automatically identified. A signal word is determined, and a pictogram is listed that requires training to understand.
The SDS signal words and the reasoning behind determining them can be confusing. This is because they are inconsistent with the Federal Insecticide, Fungicide and Rodenticide Act (FIFRA) label, which looks at other factors. There are only two GHS categories — DANGER and WARNING — whereas the FIFRA label signal words can be DANGER, WARNING or CAUTION. For pesticides, the FIFRA signal word might be CAUTION, and the SDS signal word might be DANGER, based upon different factors such as flammability not considered under FIFRA.
This causes confusion and implies that one or the other is incorrect. Realistically, they are both right, but for different purposes. Beyond that, personal protective equipment (PPE) and environmental hazards also might not be consistent. So, which PPE requirements do you follow? The U.S. Environmental Protection Agency (EPA)-approved label must be followed, at the very least.
END-USE DILUTED PRODUCTS
One question commonly asked is whether there is an end-use dilution SDS for products. After all, customers are not usually exposed to concentrate, but rather the final formulation of the product. For example, a customer might call in a panic because he read the SDS of a 10 percent concentrate, which describes a hazard that seems to be similar to certain symptoms exhibited by the family dog, but the product was in actuality used at 0.125 percent and posed no threat. Logically, dilution reduces any risk, but the SDS can depict a picture of gloom and doom.
Manufacturers are required under regulations to prepare SDS for products as shipped, not the diluted products. A diluted material SDS may be prepared as a courtesy, but it is not distributed with the name of the manufacturer because the manufacturer does not make the diluted product. It is not at all a matter of manufacturers being uncooperative, of course; it is instead a matter of regulatory mandate.
MOVING FORWARD
There are, of course, good things about SDS. There are instructions, primarily for first responders, about first aid, fighting a product fire, handling and storage, exposure, and even physical and chemical properties.
At press time, OSHA is considering updating SDS requirements, which may make them even more complicated. Regardless, SDS are an important part of pest management safety training, and every one of your employees should be prepared to answer customer questions about them. Make sure everyone understands the basics and how to explain any limitations to customers, especially those customers who panic when reading a pure-product SDS.
The post Understand the value of safety data sheets appeared first on Pest Management Professional.
from Pest Management Professional https://www.mypmp.net/2021/06/25/understand-the-value-of-safety-data-sheets/
Sacramento CA
No comments:
Post a Comment