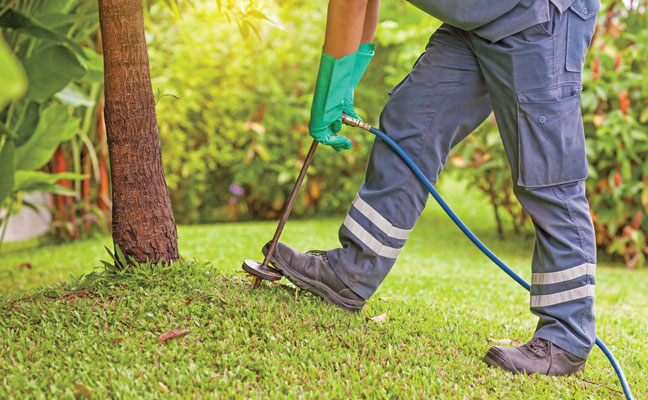
Photo: Business/iStock / Getty Images Plus/Getty Images
When I am called to evaluate how effective and safe a termite technician is conducting a subterranean termite pretreatment, I try to find out how the company conducts its own evaluations. In most cases, a skilled, experienced employee is training the technician on the job. When I ask for a detailed checklist, I am only told “Bob showed me what to do.” This might be called an exchange of techniques, right or wrong, from one person to the next.
Hopefully you have your own list of items to cover. Compare it to mine and see whether you missed any points. The answers and techniques may differ from state to state and company to company, but there must be one protocol followed consistently within the company.
Experience has taught me that four separate critique sheets are required:
- On the job.
- Pesticide label and safety data sheets (SDS).
- Management.
- Pesticide storage.
On the job
- Are there wells on or near the property? If so, how far away are they from the treatment site?
- Are there canals or other waterways near the property? If so, how far away are they from the treatment site?
- Is the weather suitable to pretreat?
- Is a spill control kit, including items to hold the pickup, available on the vehicle?
- Is the vehicle properly labeled?
- Is the vehicle registration up-to-date, and does the business registered on its title match the name used on the vehicle?
- Are the vehicle’s tires, mirrors, brakes, lights and horn in proper working condition?
- Is the applicator wearing an appropriate identification badge? If the applicator is also the driver of the vehicle, does he or she have a safe driving record?
- Is the applicator wearing the appropriate personal protective equipment (PPE), and is the PPE in working order?
- Can the applicator calculate square footage, and how long it will take to treat the site?
- Does the applicator know the volume of pesticides flowing out of the nozzle?
- What method is being used to determine the rate of discharge?
- At what time was the job started and finished? Is this reasonable, based on the volume of material used and the gallons per minute (gpm) applied?
Pesticide labels and SDS
- Are all the appropriate pesticide labels readily available?
- Are all the appropriate SDS readily available?
- Can the applicator read and understand English labels and SDS?
- When was the last time the hoses were checked to ensure
they do not leak? When were they last replaced? - Are the applicator’s fingernails short and clean? When was the last time the applicator’s gloves were checked, to ensure they are still functional?
- Is the applicator wearing the appropriate footwear for applying pesticides?
- Is the applicator wearing a long-sleeved shirt and other appropriate clothing for pesticide application? Does he or she have an extra set of clothes available if needed?
- Is the applicator’s driver’s license up to date and registered for the appropriate state?
- Is the vehicle registered with an up-to-date insurance card that is readily available?
- Are two visits scheduled to complete the job?
- Does the applicator have a cell phone or other means of contacting a supervisor in the event of an emergency?
- Does the applicator know what to do on each visit?
- What initial training (classroom and field) is given before applicators are sent out on their own?
- Is ongoing, periodic training given to applicators after they are on their own?
-
Photo: Lebazele/E+/Getty Images
Is there a written quiz on each appropriate label and SDS in the office file that includes calculating the amount of product required?
- Before starting a job, did the applicator check to ensure no one was in the target site area?
- Is there an adequate anti-siphon device in operation?
- Is a “Watch Your Step” safety sign available and in use if the applicator needs to pull a hose over a walkway?
- Did the applicator place safety cones in the front and back of the parked vehicle?
- Is a proper first-aid kit available?
- Is there an adequate measuring device available for each pesticide to be mixed?
- Is there adequate agitation in the tank to keep the pesticide properly mixed?
- What steps are taken to ensure the pesticide concentration is stored properly, so it cannot turn over and spill?
- Is the pesticide concentrate kept in a locked area when not in use?
- Is there drinking water or a similarly appropriate liquid available for the applicator?
- Does the applicator have the necessary permits to draw water from a local fire hydrant? Are the permits up to date?
- If the slab is not going to be poured immediately, are adequate steps being taken to protect the treated soil?
- Is the grade of the land sufficient that the chemical will stay where it was applied?
- Can the applicator answer what is done with the material that is left in the tank at the end of
the job? - Is the applicator able to confirm there are no detectable leaks from the pumps, hoses, etc.?
Pesticide storage area
- Is it above a flood plain level?
- Are all items stored up off of the floor?
- Is it locked when not in use?
- Is it properly ventilated with a fan where one enters the structure?
- Are all shelves and pesticide containers nonabsorbent?
- Does the local fire department have a list of what you store?
- Are all appropriate safety devices present, including but not restricted to a spill control kit, a fire extinguisher, gloves and boots?
- Are records kept of who, where, when, what and how much is issued?
- Is it labeled as containing pesticide in appropriate languages?
- Are emergency telephone numbers for all agencies available?
- Are all liquid materials stored in original containers and enclosed in containers that could contain any spills?
- Are rodenticides stored separately from insecticides?
- Is the floor non-porous?
- Is water from a sink collected in a holding tank?
- Are all pesticide containers triple-rinsed before disposal?
Quiz for applicators
- Who is your supervisor?
- How do you contact your supervisor in the event of an emergency?
- How do you know you are treating the correct lot?
- What would you do if a puddle of diluted material ended up on top of the soil?
- At what wind speed are you prohibited from treating?
- How do you get your weather report in reference to rain prior to scheduling a treatment?
- Where do you store the food you plan to eat during the day?
- Are all your buckets and containers properly labeled?
- Were you adequately trained on how to control spills?
- How are your uniforms cleaned after use?
- What do you do if the ground is frozen?
- What do you do if the water level is within two feet of the ground surface?
- What do you do if there is exposed rock on much of the surface of the ground where the slab is to be installed?
- Do you have a list of equipment and pesticides that are supposed to be on the vehicle? Are you missing anything? If so, why?
- When was the last time anyone went out with you to review how you are doing your job?
- If inspectors come up to you unannounced and say they want to watch you perform a pretreat, how should you answer them?
Quiz for managers
- Is someone in the office checking the paperwork on each pretreat to ensure the correct amount of product was applied?Per job, at what frequency are you going to conduct audits in the field and at the shop?
- Are you keeping records on the number of jobs completed per day and the time in and time out on each job?
- Is your website accurate? For example, if it states no generics are used, it’s the largest-capacity pre-treat truck in Florida, and that your company can perform specific brand-name full-house treatments — is that information still correct?
- Can your applicators calculate square feet and then correlate how long to treat a given area based on the gpm output? Can they correctly calculate the diluted material gpm of a rectangle slab design example, a one-wing-on-the-slab design example, and a two-wings-or-more slab design example?
- Are all termiticide labels and SDS up to date in the office and on the vehicles?
- When on the jobsite, if wood debris is left in the soil or wooden forms are left intact after the slab is poured, do you have a form to document it? What about for any other problems encountered?
Pesticide label quiz
- Is this product registered for preconstruction?
- What is the active ingredient?
- What is the signal word?
- Do you need to wear a respirator when mixing and applying this product?
- Do you need to wear boots when applying this product?
- Do you need to wear gloves when mixing and applying this product?
- Can you wear shorts when applying this product?
- If your skin comes into contact with this product, what should you do?
- Is there an antidote for this product?
- What do you do if you have a small spill with this product?
- How do you mix the material in the tank in reference to adding the water and concentrate?
- Who is responsible for covering the treated area?
- How far away from a well must you be to pretreat a structure in a conventional way?
- If it is scheduled to rain about one hour after you plan on finishing the job, what should you do?
The post How does your termite pretreat inspection measure up? appeared first on Pest Management Professional.
from Pest Management Professional https://www.mypmp.net/2023/07/19/how-does-your-termite-pretreat-inspection-measure-up/
Sacramento CA
No comments:
Post a Comment